往復式壓縮機工作時,曲軸帶動連桿,連桿帶動活塞,活塞做上下運動。活塞運動使氣缸內的容積發生變化,當活塞向下運動的時候,汽缸容積增大,進氣閥打開,排氣閥關閉,空氣被吸進來,完成進氣過程。
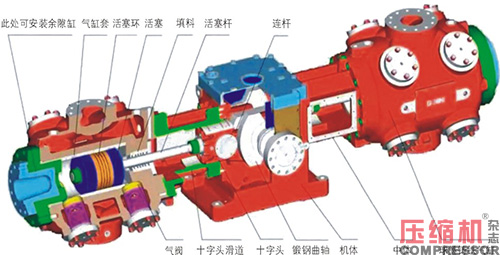
當活塞向上運動的時候,氣缸容積減小,出氣閥打開,進氣閥關閉,完成壓縮過程。通常活塞上有活塞環來密封氣缸和活塞之間的間隙,氣缸內有潤滑油潤滑活塞環。
由于往復壓縮機結構的復雜性,所以出現故障的零部件較多,引起故障的原因不一。往復壓縮機特征參數信號主要包括熱力信號、振動信號以及噪聲信號等,其中熱力信號又包括各部件溫度、排氣量、排氣壓力、氣缸內壓力等。
通過對特征信號的監測分析,識別判斷壓縮機的故障類型,是故障診斷技術的核心思想。
往復式壓縮機6大部件結構
往復式壓縮機是容積式壓縮機的一種,其主要部件包括氣缸、曲柄連桿機構、活塞組件、填料(也就是壓縮機的密封件)、氣閥、機身與基礎、管線及附屬的設備等。
1、氣缸
氣缸是壓縮機主要零部件之一,應有良好的表面以利于潤滑和耐磨,還應具有良好的導熱性,以便于使摩擦產生的熱能以最快的速度散發出去;
還要有足夠大的氣流通道面積及氣閥安裝面積,使閥腔容積達到恰好能降低氣流的壓力脈動幅度,以保證氣閥正常工作并降低功耗。余隙容積應小些,以提高壓縮機的效率。
2、曲柄連桿機構
該機構包括十字頭、連桿、曲軸、滑導等——它是主要的運轉和傳動部件件,將電機的圓周運動經連桿轉化為活塞的往復運動,同時它也是主要的受力部件。
3、活塞組件
主要有活塞頭、活塞環、托瓦和活塞桿。活塞的形狀和尺寸與氣缸有密切關系,分為雙作用和單作用活塞。活塞環用以密封氣缸內的高壓氣體,防止其從活塞和氣缸之間的間隙泄漏。
托瓦的作用顧名思義是起支撐活塞的作用,所以托瓦也是易損件,托瓦材質的好壞也直接影響壓縮機的使用壽命。
4、填料
活塞桿填料主要用于密封氣缸內座與活塞桿之間的間隙,阻止氣體沿活塞桿徑向泄漏。填料環的制造及安裝涉及“三個間隙”。
分別為軸向間隙(保證填料環在環槽內能自由浮動),徑向間隙(防止由于活塞桿的下沉使填料環受壓造成變形或者損壞)和切向間隙(用于補償填料環的磨損)。目前平面填料多為“三六瓣型”和“切向切口三瓣型”。
5、氣閥
氣閥是壓縮機最主要的組件,同時也是最容易損壞的零件。其設計的好壞會直接影響到壓縮機的排氣量、功耗及運轉可靠性。
好的氣閥應具有以下特點:高效節能(占軸功率的3%~7%),氣密性與動作及時性完美結合,壽命長(一般實際壽命8000h),形成的余隙容積小,噪音低,溫升小,可翻新使用。目前氣閥的材質分為金屬和非金屬,就目前的情況看,非金屬材料閥片的應用越來越廣泛。
6、管線和附屬設備
壓縮機的管路和出入緩沖器的設計是否合理,將直接影響機組的振動情況。

往復式壓縮機5大故障診斷監測辦法
目前,往復式壓縮機的故障診斷監測方法主要有以下幾種:
1、熱力性能監測法
溫度是往復壓縮機較為敏感的特征參數,監測溫度的變化可以了解壓縮機內部零部件的工作狀態,如排氣閥漏氣,在吸氣過程會出現倒吸現象,導致氣閥溫度升高;活塞桿拉傷,填料函的溫度也會升高等。
使用溫度監測方法時,傳感器可置于機體外側,不需改變殼體結構,操作方便。
往復壓縮機一個運動周期包括吸氣、壓縮、排氣、膨脹4個過程,壓力在4個過程中呈周期性變化,缸內壓力變化曲線可直接反應壓縮機是否正常運行。如吸氣閥泄漏,吸氣過程壓力延長,排氣過程縮短,膨脹過程曲線也會下移。
由于壓力測點位于缸內,在缸蓋或殼體其它位置要預留安裝孔,這是壓力監測的需要特別注意的地方。
2、振動監測法
振動信號也是往復壓縮機故障診斷的一個敏感特征參數,如氣閥損壞、活塞桿下沉、十字頭螺栓松動、連桿磨損等大多數故障均伴隨著振動信號的異常。
基于越來越成熟的信號分析技術,對往復壓縮機非穩態振動信號的研究工作也越來越多,如通過加速度傳感器測十字頭滑道箱、汽缸側壁、汽缸蓋、軸承等處的振動信號來診斷動力性故障,是一種比較有效的方法。
3、位移監測法
往復壓縮機活塞桿斷裂通常會引起其他零部件的破壞,嚴重時甚至會引起機組爆炸。活塞桿斷裂是瞬間發生的,斷裂之前的裂紋監測非常困難,只能對斷裂部位做事后分析,目前還沒有可靠有效的診斷預警方法。通過安裝位移傳感器,監測活塞桿的沉降量,間接了解活塞環、十字頭等的磨損狀況,可以作為一種輔助手段。
4、油液監測法
油液監測是通過對壓縮機潤滑油進行油液分析,檢測樣品內磨損顆粒的大小、形狀、成分等,是一種比較理想的輔助手段。如用鐵譜分析、光譜分析、顆粒計數等監測空壓機運動副的磨損情況等。有學者通過檢測油品中的銅元素含量,發現大頭瓦碎裂,成功避免了事故的發生。
5、噪聲監測法
噪聲信號中有機械設備運行的信號,也包含周圍環境及其它噪聲源的信號,因此,噪聲監測在往復壓縮機故障診斷中也可以作為一種可靠的輔助手段。結合先進的噪聲傳感器,分離提取典型故障噪聲信號,是往復壓縮機故障診斷領域未來研究的一個熱點和難點。
往復壓縮機故障種類繁多,一個故障會引起多個特征參數的變化,因此在故障診斷過程中應該綜合考慮多參數之間的關聯性,以便更精確地識別故障類型。此外,人工智能系統和神經網絡技術也越來越多的應用在往復壓縮機故障診斷系統中,使故障診斷技術達到了智能化的高度。
按往復壓縮機引起事故的零部件不同分類,各類故障所占的比例如下圖所示。其中,吸、排氣閥故障概率最高,達到36%;其次,填料函、連桿、活塞桿等引起的事故所占比例也挺高。

表1給出了常見故障類型及所采用監測診斷方法,為往復壓縮機故障診斷提供一個參考。

往復式壓縮機10大常見故障及處理辦法
1、吸氣閥泄露或者密封墊片損壞
吸氣閥泄漏或者密封墊片損壞主要表現為:(1)溫升高,閥蓋發熱;(2)對應的排氣閥溫度升高;(3)閥所在級與前一級間壓力升高;(4)壓縮機排氣量下降;(5)進氣溫度升高。
氣體經過壓縮后溫度上升,吸氣閥泄漏或者密封墊片損壞后,高溫氣體返回進氣腔,造成閥溫升高,進氣溫度上升,從而再次被壓縮后排氣溫度升高。另外,壓縮后的氣體回流造成前面壓力升高,壓力越升高排氣量下降就越多。
2、排氣閥泄漏或密封墊墊片損壞
排氣閥泄漏或者密封墊片損壞主要表現為:
(1)排氣閥溫度升高,閥片發熱;(2)排氣壓力下降;(3)壓縮機排氣量下降。
由于排氣閥泄漏或者密封墊片損壞。在氣缸吸氣過程中,部分壓縮后的高溫高壓氣體回流至氣缸使混合氣體溫度升高,再次被壓縮后溫度更高,回流還造成流量下降,排氣壓力下降。
3、負荷調節機構卡澀
負荷調節機構卡澀主要表現為:(1)負荷調節指示器不動作;(2)對應的進氣閥溫度升高,閥蓋發熱;(3)對應的排氣閥溫升高;(4)閥所在級與前一級間壓力升高;(5)壓縮機排氣量下降;(6)進氣溫度升高。
負荷調節機構如果卡在泄荷的位置會造成吸氣閥泄漏;如果卡在加載位置上則會造成壓縮機負載啟動,影響傳動部件的使用壽命。
4、活塞環常見的故障有
(1)活塞環斷裂;(2)活塞環漲死,失去彈性,不能膨脹;(3)活塞環過度磨損,間隙增大。
活塞環不能起到密封作用的主要表現形式為:
(1)該級排氣溫度升高;(2)該級排氣壓力降低;(3)壓縮機排氣量下降。
對于雙作用往復壓縮機,即氣缸內一側在壓縮時,另一側在吸氣,當活塞環損壞或者漲死時,不能起到密封作用,使得蓋側或軸側被壓縮的高壓高溫氣體通過活塞環竄入軸側(或蓋側)低溫低壓氣體中。
與吸入的低壓溫氣體混合,混合之后氣體溫度升高,又由于壓縮氣體通過活塞環互竄,使該級的排氣壓力下降,壓縮機的排氣也隨之下降。
5、工藝介質夾帶顆粒物
現場檢查有時會發現在壓縮機氣缸及填料密封腔體中有大量沉積物。這些沉積物是由工藝介質夾帶過來的微細固體粉塵或結焦的碳粒組成,其硬度往往很高。
其在密封腔處的沉積必然會造成密封填料嚴重的磨損,從而大大縮短填料密封環及活塞桿的使用壽命。通過調整工藝使壓縮機參數達到設計要求,必要時可加氣固分離器分離掉這些顆粒雜物,就可避免氣缸與活塞環、活塞桿與填料摩擦副之間的顆粒磨損。
6、活塞桿組合密封環緊箍力過大或彈簧失彈
往復式壓縮機活塞桿與填料密封處于相對運動狀態,填料環通過抱緊活塞桿來實現對介質的密封,填料環的抱緊力由彈簧及環徑向壓差來實現。
顯然,彈簧的緊箍力越大,填料對活塞桿的抱緊力就越大,活塞桿與填料環的相對摩擦就會越嚴重,摩擦產生的熱量就越多,從而造成填料環使用初期溫升非常高,磨損特別厲害。
由于填料環常用填充聚四氟乙烯制成,其熱膨脹系數較大,初始階段產生的摩擦熱量若不能被及時帶走,填料環熱膨脹變形大,加上填料環彈簧緊箍力大,摩擦磨損加劇,形成惡性循環。經過短短幾天的劇烈磨損,當填料對活塞桿的抱緊力趨于減小即摩擦力減小時填料環與活塞桿之間的縫隙增大,介質泄漏量增加,最終密封失效。
解決辦法是在總體結構不變的前提下,更換活塞密封環調整活塞密封環與缸體之間的間隙或采用具有自潤滑性能,耐磨性能更好的材料制作活塞環和填料環,再者可適當降低彈簧緊箍力,設計引入間隙密封。
彈簧的失彈大多是由于彈簧疲勞所導致,彈簧質量問題只占少數情況,只能更換質量好些的彈簧。
7、填料密封盒冷卻水流量偏小
填料密封盒部位的溫升主要是由于填料環與活塞桿劇烈摩擦引起的,這些摩擦熱應被及時帶走。實際上,由于填料密封盒用水與缸套用水基本都采用并聯形式,填料密封處的壓降大,因而導致填料盒冷卻水流量不夠,摩擦熱不能被及時帶走,影響了填料的正常使用壽命。
因此,應適當增大循環水壓力及流量以使循環水及時帶走活塞桿與填料環摩擦產生的熱量。控制填料密封盒處的溫度不大于60℃。
8、填料密封處注油量過小或過大
注油量過大容易造成過多的油乳化,形成沉積物;過小則填料環潤滑效果不好,磨損速度加快,影響使用壽命。
注油量的確定除了按廠家的標準注入外,還應該在試車初期,通過檢查密封環處的運行情況,確定一個合適的量。試車結束后,打開檢查填料處活塞桿上有無碳狀物,以判斷注油量的大小。
9、管路振動導致故障
引起往復壓縮機及其管線振動的原因主要有兩類:一類是由機組振動的不平衡基礎設計不當而引起。壓縮機在組裝過程中由于技術或質量問題造成機組裝配誤差大,引起機組的平衡惡化產生振動。
壓縮機基礎質量太小也可引起壓縮機本體振動。另一類是由管線內氣流脈動引起活塞式壓縮機吸氣和排氣的間隙變化,可使氣體產生脈動——壓縮機管線內充滿氣體時形成氣柱。該氣柱是一個有連續質量的彈性振動系統,受到一定工況條件的誘導就會發生振動——在機組管系的彎頭處氣體運動方向會發生改變,從而使管線受到氣體沖擊力的作用。
系統管線彎頭太多、管線受到的沖擊力就會很大。如果彎頭處缺少固定支點,將會產生劇烈振動。當流體穩定流動時,管線不產生振動;但當流體運動方向在管線斷面突變處變化時,流體速度發生變化,導致管線受力改變——使管線內局部壓力變化,產生一定的脈動,誘發振動。
如果管內有脈動存在,則管線內各部分的壓力不同,也會形成振源。由于管系內彎頭較多,流體在管線內不斷地改變流動方向,對管線形成沖擊;并且流體自身的狀態也發生變化——這些變化誘發的振動,其頻率與管系固有頻率重合時,則產生共振。
消除共振最基本的方法是將氣流脈動壓力減小,并將其固定在允許的最小值之內,使激發頻率不等于管路固有頻率。具體方法有:
(1)在緊靠壓縮機每一級出入口處各設置一個緩沖罐,改變管系的氣柱固有頻率,破壞振源與管系振動頻率的重合,并可降低氣流脈動的幅值。但是緩沖罐容積設計不好也會引起振動,經驗表明其應該比氣缸行程容積大10倍,且盡量靠近氣缸;
(2)在管系的適當位置,特別是管線的彎頭處增設固定支撐,并在管線與支點間加墊硬橡膠板以改變支撐彈性并改變管系的振動頻率;
(3)在管線的適當位置增設孔板,以改變管系的振動頻率,用孔板減振會伴有較大阻力損失,因此只用于已發生共振且無法改變截面的情況,其作用遠不及緩沖罐的作用。
10、撞缸
撞缸是往復機組的重大惡性事故,主要表現為缸體內發生巨大的撞擊聲,嚴重時導致機組多處損壞,如缸蓋撞飛,大小頭瓦斷裂甚至發生爆炸。
撞缸分為液擊和金屬撞擊兩種,液擊聲音比金屬撞擊聲要沉悶一些,但是后果一樣嚴重。防范措施主要是規范日常操作防止大量帶液;加強巡檢,發現異常聲音及時排查。
來源:本站原創
往復式壓縮機工作時,曲軸帶動連桿,連桿帶動活塞,活塞做上下運動。活塞運動使氣缸內的容積發生變化,當活塞向下運動的時候,汽缸容積增大,進氣閥打開,排氣閥關閉,空氣被吸進來,完成進氣過程。
當活塞向上運動的時候,氣缸容積減小,出氣閥打開,進氣閥關閉,完成壓縮過程。通常活塞上有活塞環來密封氣缸和活塞之間的間隙,氣缸內有潤滑油潤滑活塞環。
由于往復壓縮機結構的復雜性,所以出現故障的零部件較多,引起故障的原因不一。往復壓縮機特征參數信號主要包括熱力信號、振動信號以及噪聲信號等,其中熱力信號又包括各部件溫度、排氣量、排氣壓力、氣缸內壓力等。
通過對特征信號的監測分析,識別判斷壓縮機的故障類型,是故障診斷技術的核心思想。
往復式壓縮機6大部件結構
往復式壓縮機是容積式壓縮機的一種,其主要部件包括氣缸、曲柄連桿機構、活塞組件、填料(也就是壓縮機的密封件)、氣閥、機身與基礎、管線及附屬的設備等。
1、氣缸
氣缸是壓縮機主要零部件之一,應有良好的表面以利于潤滑和耐磨,還應具有良好的導熱性,以便于使摩擦產生的熱能以最快的速度散發出去;
還要有足夠大的氣流通道面積及氣閥安裝面積,使閥腔容積達到恰好能降低氣流的壓力脈動幅度,以保證氣閥正常工作并降低功耗。余隙容積應小些,以提高壓縮機的效率。
2、曲柄連桿機構
該機構包括十字頭、連桿、曲軸、滑導等——它是主要的運轉和傳動部件件,將電機的圓周運動經連桿轉化為活塞的往復運動,同時它也是主要的受力部件。
3、活塞組件
主要有活塞頭、活塞環、托瓦和活塞桿。活塞的形狀和尺寸與氣缸有密切關系,分為雙作用和單作用活塞。活塞環用以密封氣缸內的高壓氣體,防止其從活塞和氣缸之間的間隙泄漏。
托瓦的作用顧名思義是起支撐活塞的作用,所以托瓦也是易損件,托瓦材質的好壞也直接影響壓縮機的使用壽命。
4、填料
活塞桿填料主要用于密封氣缸內座與活塞桿之間的間隙,阻止氣體沿活塞桿徑向泄漏。填料環的制造及安裝涉及“三個間隙”。
分別為軸向間隙(保證填料環在環槽內能自由浮動),徑向間隙(防止由于活塞桿的下沉使填料環受壓造成變形或者損壞)和切向間隙(用于補償填料環的磨損)。目前平面填料多為“三六瓣型”和“切向切口三瓣型”。
5、氣閥
氣閥是壓縮機最主要的組件,同時也是最容易損壞的零件。其設計的好壞會直接影響到壓縮機的排氣量、功耗及運轉可靠性。
好的氣閥應具有以下特點:高效節能(占軸功率的3%~7%),氣密性與動作及時性完美結合,壽命長(一般實際壽命8000h),形成的余隙容積小,噪音低,溫升小,可翻新使用。目前氣閥的材質分為金屬和非金屬,就目前的情況看,非金屬材料閥片的應用越來越廣泛。
6、管線和附屬設備
壓縮機的管路和出入緩沖器的設計是否合理,將直接影響機組的振動情況。
往復式壓縮機5大故障診斷監測辦法
目前,往復式壓縮機的故障診斷監測方法主要有以下幾種:
1、熱力性能監測法
溫度是往復壓縮機較為敏感的特征參數,監測溫度的變化可以了解壓縮機內部零部件的工作狀態,如排氣閥漏氣,在吸氣過程會出現倒吸現象,導致氣閥溫度升高;活塞桿拉傷,填料函的溫度也會升高等。
使用溫度監測方法時,傳感器可置于機體外側,不需改變殼體結構,操作方便。
往復壓縮機一個運動周期包括吸氣、壓縮、排氣、膨脹4個過程,壓力在4個過程中呈周期性變化,缸內壓力變化曲線可直接反應壓縮機是否正常運行。如吸氣閥泄漏,吸氣過程壓力延長,排氣過程縮短,膨脹過程曲線也會下移。
由于壓力測點位于缸內,在缸蓋或殼體其它位置要預留安裝孔,這是壓力監測的需要特別注意的地方。
2、振動監測法
振動信號也是往復壓縮機故障診斷的一個敏感特征參數,如氣閥損壞、活塞桿下沉、十字頭螺栓松動、連桿磨損等大多數故障均伴隨著振動信號的異常。
基于越來越成熟的信號分析技術,對往復壓縮機非穩態振動信號的研究工作也越來越多,如通過加速度傳感器測十字頭滑道箱、汽缸側壁、汽缸蓋、軸承等處的振動信號來診斷動力性故障,是一種比較有效的方法。
3、位移監測法
往復壓縮機活塞桿斷裂通常會引起其他零部件的破壞,嚴重時甚至會引起機組爆炸。活塞桿斷裂是瞬間發生的,斷裂之前的裂紋監測非常困難,只能對斷裂部位做事后分析,目前還沒有可靠有效的診斷預警方法。通過安裝位移傳感器,監測活塞桿的沉降量,間接了解活塞環、十字頭等的磨損狀況,可以作為一種輔助手段。
4、油液監測法
油液監測是通過對壓縮機潤滑油進行油液分析,檢測樣品內磨損顆粒的大小、形狀、成分等,是一種比較理想的輔助手段。如用鐵譜分析、光譜分析、顆粒計數等監測空壓機運動副的磨損情況等。有學者通過檢測油品中的銅元素含量,發現大頭瓦碎裂,成功避免了事故的發生。
5、噪聲監測法
噪聲信號中有機械設備運行的信號,也包含周圍環境及其它噪聲源的信號,因此,噪聲監測在往復壓縮機故障診斷中也可以作為一種可靠的輔助手段。結合先進的噪聲傳感器,分離提取典型故障噪聲信號,是往復壓縮機故障診斷領域未來研究的一個熱點和難點。
往復壓縮機故障種類繁多,一個故障會引起多個特征參數的變化,因此在故障診斷過程中應該綜合考慮多參數之間的關聯性,以便更精確地識別故障類型。此外,人工智能系統和神經網絡技術也越來越多的應用在往復壓縮機故障診斷系統中,使故障診斷技術達到了智能化的高度。
按往復壓縮機引起事故的零部件不同分類,各類故障所占的比例如下圖所示。其中,吸、排氣閥故障概率最高,達到36%;其次,填料函、連桿、活塞桿等引起的事故所占比例也挺高。
表1給出了常見故障類型及所采用監測診斷方法,為往復壓縮機故障診斷提供一個參考。
往復式壓縮機10大常見故障及處理辦法
1、吸氣閥泄露或者密封墊片損壞
吸氣閥泄漏或者密封墊片損壞主要表現為:(1)溫升高,閥蓋發熱;(2)對應的排氣閥溫度升高;(3)閥所在級與前一級間壓力升高;(4)壓縮機排氣量下降;(5)進氣溫度升高。
氣體經過壓縮后溫度上升,吸氣閥泄漏或者密封墊片損壞后,高溫氣體返回進氣腔,造成閥溫升高,進氣溫度上升,從而再次被壓縮后排氣溫度升高。另外,壓縮后的氣體回流造成前面壓力升高,壓力越升高排氣量下降就越多。
2、排氣閥泄漏或密封墊墊片損壞
排氣閥泄漏或者密封墊片損壞主要表現為:
(1)排氣閥溫度升高,閥片發熱;(2)排氣壓力下降;(3)壓縮機排氣量下降。
由于排氣閥泄漏或者密封墊片損壞。在氣缸吸氣過程中,部分壓縮后的高溫高壓氣體回流至氣缸使混合氣體溫度升高,再次被壓縮后溫度更高,回流還造成流量下降,排氣壓力下降。
3、負荷調節機構卡澀
負荷調節機構卡澀主要表現為:(1)負荷調節指示器不動作;(2)對應的進氣閥溫度升高,閥蓋發熱;(3)對應的排氣閥溫升高;(4)閥所在級與前一級間壓力升高;(5)壓縮機排氣量下降;(6)進氣溫度升高。
負荷調節機構如果卡在泄荷的位置會造成吸氣閥泄漏;如果卡在加載位置上則會造成壓縮機負載啟動,影響傳動部件的使用壽命。
4、活塞環常見的故障有
(1)活塞環斷裂;(2)活塞環漲死,失去彈性,不能膨脹;(3)活塞環過度磨損,間隙增大。
活塞環不能起到密封作用的主要表現形式為:
(1)該級排氣溫度升高;(2)該級排氣壓力降低;(3)壓縮機排氣量下降。
對于雙作用往復壓縮機,即氣缸內一側在壓縮時,另一側在吸氣,當活塞環損壞或者漲死時,不能起到密封作用,使得蓋側或軸側被壓縮的高壓高溫氣體通過活塞環竄入軸側(或蓋側)低溫低壓氣體中。
與吸入的低壓溫氣體混合,混合之后氣體溫度升高,又由于壓縮氣體通過活塞環互竄,使該級的排氣壓力下降,壓縮機的排氣也隨之下降。
5、工藝介質夾帶顆粒物
現場檢查有時會發現在壓縮機氣缸及填料密封腔體中有大量沉積物。這些沉積物是由工藝介質夾帶過來的微細固體粉塵或結焦的碳粒組成,其硬度往往很高。
其在密封腔處的沉積必然會造成密封填料嚴重的磨損,從而大大縮短填料密封環及活塞桿的使用壽命。通過調整工藝使壓縮機參數達到設計要求,必要時可加氣固分離器分離掉這些顆粒雜物,就可避免氣缸與活塞環、活塞桿與填料摩擦副之間的顆粒磨損。
6、活塞桿組合密封環緊箍力過大或彈簧失彈
往復式壓縮機活塞桿與填料密封處于相對運動狀態,填料環通過抱緊活塞桿來實現對介質的密封,填料環的抱緊力由彈簧及環徑向壓差來實現。
顯然,彈簧的緊箍力越大,填料對活塞桿的抱緊力就越大,活塞桿與填料環的相對摩擦就會越嚴重,摩擦產生的熱量就越多,從而造成填料環使用初期溫升非常高,磨損特別厲害。
由于填料環常用填充聚四氟乙烯制成,其熱膨脹系數較大,初始階段產生的摩擦熱量若不能被及時帶走,填料環熱膨脹變形大,加上填料環彈簧緊箍力大,摩擦磨損加劇,形成惡性循環。經過短短幾天的劇烈磨損,當填料對活塞桿的抱緊力趨于減小即摩擦力減小時填料環與活塞桿之間的縫隙增大,介質泄漏量增加,最終密封失效。
解決辦法是在總體結構不變的前提下,更換活塞密封環調整活塞密封環與缸體之間的間隙或采用具有自潤滑性能,耐磨性能更好的材料制作活塞環和填料環,再者可適當降低彈簧緊箍力,設計引入間隙密封。
彈簧的失彈大多是由于彈簧疲勞所導致,彈簧質量問題只占少數情況,只能更換質量好些的彈簧。
7、填料密封盒冷卻水流量偏小
填料密封盒部位的溫升主要是由于填料環與活塞桿劇烈摩擦引起的,這些摩擦熱應被及時帶走。實際上,由于填料密封盒用水與缸套用水基本都采用并聯形式,填料密封處的壓降大,因而導致填料盒冷卻水流量不夠,摩擦熱不能被及時帶走,影響了填料的正常使用壽命。
因此,應適當增大循環水壓力及流量以使循環水及時帶走活塞桿與填料環摩擦產生的熱量。控制填料密封盒處的溫度不大于60℃。
8、填料密封處注油量過小或過大
注油量過大容易造成過多的油乳化,形成沉積物;過小則填料環潤滑效果不好,磨損速度加快,影響使用壽命。
注油量的確定除了按廠家的標準注入外,還應該在試車初期,通過檢查密封環處的運行情況,確定一個合適的量。試車結束后,打開檢查填料處活塞桿上有無碳狀物,以判斷注油量的大小。
9、管路振動導致故障
引起往復壓縮機及其管線振動的原因主要有兩類:一類是由機組振動的不平衡基礎設計不當而引起。壓縮機在組裝過程中由于技術或質量問題造成機組裝配誤差大,引起機組的平衡惡化產生振動。
壓縮機基礎質量太小也可引起壓縮機本體振動。另一類是由管線內氣流脈動引起活塞式壓縮機吸氣和排氣的間隙變化,可使氣體產生脈動——壓縮機管線內充滿氣體時形成氣柱。該氣柱是一個有連續質量的彈性振動系統,受到一定工況條件的誘導就會發生振動——在機組管系的彎頭處氣體運動方向會發生改變,從而使管線受到氣體沖擊力的作用。
系統管線彎頭太多、管線受到的沖擊力就會很大。如果彎頭處缺少固定支點,將會產生劇烈振動。當流體穩定流動時,管線不產生振動;但當流體運動方向在管線斷面突變處變化時,流體速度發生變化,導致管線受力改變——使管線內局部壓力變化,產生一定的脈動,誘發振動。
如果管內有脈動存在,則管線內各部分的壓力不同,也會形成振源。由于管系內彎頭較多,流體在管線內不斷地改變流動方向,對管線形成沖擊;并且流體自身的狀態也發生變化——這些變化誘發的振動,其頻率與管系固有頻率重合時,則產生共振。
消除共振最基本的方法是將氣流脈動壓力減小,并將其固定在允許的最小值之內,使激發頻率不等于管路固有頻率。具體方法有:
(1)在緊靠壓縮機每一級出入口處各設置一個緩沖罐,改變管系的氣柱固有頻率,破壞振源與管系振動頻率的重合,并可降低氣流脈動的幅值。但是緩沖罐容積設計不好也會引起振動,經驗表明其應該比氣缸行程容積大10倍,且盡量靠近氣缸;
(2)在管系的適當位置,特別是管線的彎頭處增設固定支撐,并在管線與支點間加墊硬橡膠板以改變支撐彈性并改變管系的振動頻率;
(3)在管線的適當位置增設孔板,以改變管系的振動頻率,用孔板減振會伴有較大阻力損失,因此只用于已發生共振且無法改變截面的情況,其作用遠不及緩沖罐的作用。
10、撞缸
撞缸是往復機組的重大惡性事故,主要表現為缸體內發生巨大的撞擊聲,嚴重時導致機組多處損壞,如缸蓋撞飛,大小頭瓦斷裂甚至發生爆炸。
撞缸分為液擊和金屬撞擊兩種,液擊聲音比金屬撞擊聲要沉悶一些,但是后果一樣嚴重。防范措施主要是規范日常操作防止大量帶液;加強巡檢,發現異常聲音及時排查。
來源:本站原創
網友評論
條評論
最新評論